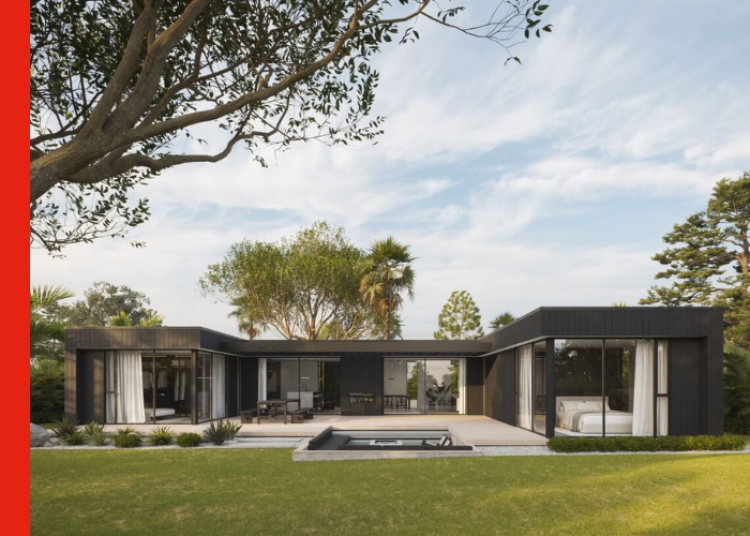
Bespoke prebuilt Lake Tarawera home by Nook Homes
Building a house in a factory is a fantastic way to create a high-quality home without being delayed by bad weather.
As materials and processes become more streamlined, prebuilt homes are providing more choice for buyers, more efficiency, and even faster delivery.
REDnews takes a look at trends and developments in the prebuilt industry, which has matured considerably in recent years.
Smaller homes are gaining popularity
The trend toward larger homes peaked in 2010 but ever since, the size of the average new build has been falling. Kiwis are now looking for affordable, liveable options.
“We’ve definitely been building more smaller homes in the past six months,” says Sam Paterson, Director at Transbuild.
“We see parents with rural properties adding minor dwellings for their kids, enabling them to get onto the property ladder. We also see multigenerational living, where secondary homes are used for parents.”
Nook Homes director Jade Stack says the homes they deliver are more commonly in the 100 to 190m2 range. Stack said Nook saw a lot of customers downsizing from the 300m2 homes that used to be all the rage.
Sarah Smith, Sales and Marketing Manager at Lockwood Homes has also noticed this pattern, with greater demand for three-bedroom homes of around 100m2 to 130m2. Smaller two-bedroom homes are also popular, and the number of enquiries about one-bedroom homes means the company is adding this option to its prebuilt range.
“People know the cost of housing is huge,” she says, “so if they can get something that they own, that’s what they want. It might be small, but it’s theirs, and that’s what’s important.”
Greater customisation now available
Off-site builds now offer greater customisation than they have in the past and high-end architectural designs are now commonplace.
While most prebuilt houses are placed on piles, Nook Homes is now offering architectural-style houses built on concrete slabs for the close-to-the-ground aesthetic and the option of having a polished concrete floor.
Smith says at Lockwood, demand from buyers has led to more choices and options when it comes to the finished product.
“There’s a big desire from clients to customise the fit-out of their home to suit their tastes. From the kitchens to the lighting, there’s a range of customisation available that can be added to the set design options. We’re finding people are often prepared to spend time and money to upgrade, so they can get the finishes they really want.”
There has also been growing interest in solar energy capture systems and even off-grid living, adds Smith; these aren’t manufactured into the build but can be planned for and then added onsite.
Structurally-insulated panels are improving efficiencies
All new buildings now need to be better insulated to meet the H1 energy efficiency standards that came into force on November 1, 2023. With warmer and better-sealed homes, demand for ventilation systems has also increased.
“Heat recovery systems and ventilation systems keep a well-sealed warm house from getting that damp feeling,” says Jade McNamara, Managing Director at Exceed Homes.
“We can now incorporate those into the design of a house, and build in ducted systems when we manufacture it.”
One important way that prebuilt homes deliver to higher insulation requirements is through the use of structurally-insulated panels (SIPs), an alternative to traditional timber-framed construction.
Structurally-insulated panels sandwich a core of acoustic and thermal insulation between two layers of board. SIPs outperform traditional framing ratings for insulation, and they’re eco-friendly.
“This is technology that they’ve been using for decades in Europe, but it’s in its infancy in New Zealand,” Exceed’s McNamara explains.
“The SIPS panels are really good for warmth. We built a SIPs panel house in Middlemarch [in the lower South Island], which gets well below zero in winter, and the clients told us their house never dropped below 19 or 20 degrees - they didn’t need to turn on the heater. That’s what everyone is pushing for these days.”
Pricing certainty and speed provide value for money
Since the supply chain chaos of the pandemic, traditional on-site construction companies have been understandably reluctant to offer fixed-price contracts. With an offsite build, however, buyers can still get some price certainty – a welcome prospect with inflation running high.
“We do fixed-price contracts and buyers appreciate that,” says Transbuild’s Paterson.
“It means they don’t get halfway through the build and realise they’ve gone over budget. But the main benefits with our product are speed, and constructing the home while the consents are processing.
“What’s really innovative is the way we factory assemble the buildings – it’s faster, more economical and more sustainable. By using specialist offsite factory assembly crews we’ve seen big improvements over the past 12 months.
“Eight weeks for the construction of the home saves the client at least six months of building time, which means spending less on both financing costs and delays caused by the weather.”
Smith says recent media coverage of small businesses failing has been scary for people who considering a new build. That’s led to Lockwood offering a deed of security to clients over their offsite builds “so if anything happens they have full rights to come in and take it before anyone else.”
“We want to reassure customers that we’ll do everything we can do make sure they have security.”
Offsite building is forecast to boom
Given all the advantages of prefabricated building, it’s no surprise that its popularity is growing in Aotearoa. Paterson says prebuilt homes are already the smart choice in regions where tradies are in short supply, such as Northland’s holiday hotspots.
You can build your beach house in a factory and then have it delivered to site. If you live elsewhere, it’s much easier to only project manage the final 20% of the build rather than the entire onsite construction process.
“The younger generation are looking for new innovative ways and faster ways to get houses, so offsite construction is definitely more in the media and in the market,” says Paterson.
“There are more suppliers and options now, which is a good thing. People are starting to understand the high level of quality you can achieve in a controlled environment.”
Photographs 1 and 2 supplied by Nook Homes